Industries
Foundry – Die Casting & Sand Casting
The life of die casting molds can be extended considerably with the Armoloy process. When the Armoloy treatment is applied early in the life of the die, the number of castings made from the die can be increased and more profits generated. Armoloy Thin Dense Chome (TDC) dramatically increases the wear life of patterns and molds by increasing the hardness and lubricity of standard mold materials (P20 and H-13).
By increasing the surface hardness without creating distortion of the base material, the pattern or corebox will see a significant increase in production. The coating also increases the lubricity by reducing the coefficient of friction by 25 – 50% which means less mold release and less fighting to remove the mold pattern itself. Both the hardness and lubricity generates higher yields of patterns with less downtime. Armoloy TDC can be stripped and reapplied, creating a preventive maintenance program to achieve the highest efficiencies of the overall life of a pattern or corebox for sand castings.
Please visit our Resources page for more information on how Armoloy TDC can be used in foundry applications.
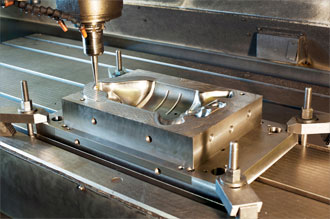
Die Casting & Sand Casting
“This affordable material is nothing short of amazing – a true chrome material that wears and wears. When it gets a little thin, it can be easily removed and replaced at the original thickness very quickly at room temperature. Dimensional accuracy maintained at less than .0003” per side for thickness. We have seen core box life extended 5 times versus uncoated boxes.”
Jack Palmer
Palmer Manufacturing & Supply
Food Processing
Armoloy TDC makes food processing equipment last longer and clean up faster. Armoloy is USDA approved. Corrosion can be reduced and/or eliminated in most applications. The low coefficient of friction created by Armoloy allows for reduced wear and less maintenance downtime. The lubricious nature of the coating combined with outstanding wear capabilities (78Rc) allow food processing equipment to operate better and withstand daily wash-downs and cleaning. Armoloy can be applied to all grades of stainless steel and can eliminate the need for Teflon or other nondurable surface coatings.
Armoloy TDC is approved for food contact applications by the USDA, and considered safe for food contact by the FDA. The coatings are able to withstand temperatures up to 1,650°F.
The coatings’ resistance to corrosion caused by daily wash-downs assists in reducing maintenance downtime. Applying the coating to stainless steel results in magnitudes of corrosion resistance much greater than either stainless steel or coated tool steel.
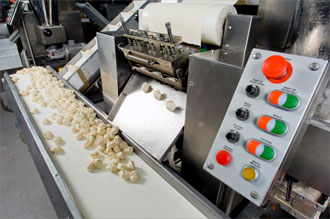
Food Processing
Armoloy's corrosion resistance for the food processing industry has been proven in our case study.
General Manufacturing
Armoloy TDC has a wide variety of uses throughout the manufacturing world. Creating less down time and increasing efficiencies is something that we all try to achieve on a daily basis. Armoloy TDC creates longer lasting parts, tooling, and assemblies for any industry. From shafting, bushings, and even pumps, Armoloy TDC has significantly increased the wear life and overall generated substantial cost savings for even the smallest of parts. Armoloy TDC is able to achieve this success due to its 78Rc surface hardness and increased lubricity which reduces the coefficient of friction by 25 – 50%.
Armoloy TDC is a low temperature surface treatment that is applied at 135°F. There is no distortion or molecular change to the part. Holding tolerance at .0001” – .0003”, there is no need to grind or polish after the coating is applied. Controlled deposits are applied allowing the coatings to work against themselves in metal-to-metal movement applications.
Please visit our Resources page for more information on the multiple applications for Armoloy TDC.
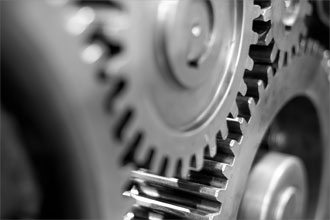
General Manufacturing
Firearms
Armoloy of Ohio has been providing quality firearm coatings for over 20 years. The coating has proven time and time again to be an optimal coating for firearms and has been praised as “one of the best rust-resistant metal finishes for handguns, shotguns, and rifles.” Armoloy technology is unlike any other conventional chromium coating. Our proprietary process and coating conforms to existing metal surfaces with amazing detail, creating a hard, slippery, and corrosive resistant surface. It will not chip, flake, crack, peel or separate from the base material even under the most rugged conditions. Armoloy’s thickness, with regard to steel, remains constant and predictable and will not reflect a buildup of greater than 0.0002 of an inch or about one fourth the thickness of a human hair! It has an equivalent hardness in excess of 78 Rockwell C when measured by conventional micro-hardness methods, making it one of the hardest coatings on the market.
- Nickel and chrome weapons must be stripped prior to processing.
- Red inserts on front sights are not affected by the Armoloy® process. We suggest that you break your weapon in and have your trigger action to your specifications prior to applying the Armoloy® finish.
- We strongly advise against applying the Armoloy® coating to springs, and we do not plate alloy (aluminum) parts, due to the possibility of damage to your firearm.
Guns must be disassembled prior to sending to Armoloy of Ohio, Inc.
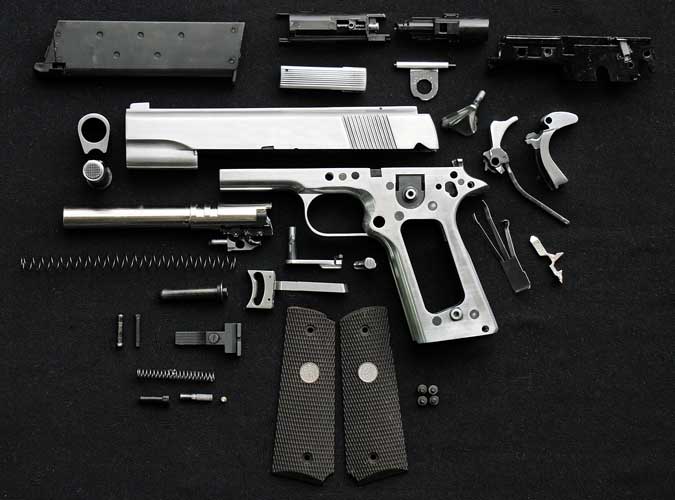