Better Performance with Chromium Coatings and Industrial Lubricants
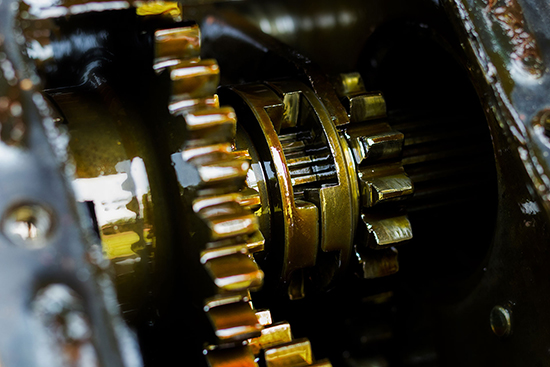
The combination of lubricants and chromium coatings plays a pivotal role in enhancing the performance and longevity of machinery. The type of lubricants used and how systems incorporate it vary based on the kind of device, the operating environment, and other factors. Their effectiveness is significantly amplified when used in conjunction with chromium coatings.
Types of Lubricants:
Greases: Comprised of oils like mineral oil, mixed with thickening agents, greases are essential in providing tackiness and other desirable properties. When paired with chromium coatings, their ability to protect and lubricate surfaces is notably increased.
Oils: These natural lubricants, often enhanced with additives to combat oxidation and corrosion, show improved performance when used on surfaces coated with chromium. This combination greatly extends the life of machinery parts.
Dry Lubricants: In environments with extreme temperatures or pressures where liquid lubricants fail, dry lubricants, or dry film lubricants, like graphite and molybdenum come into play. Their effectiveness is significantly boosted when applied to chromium-coated surfaces.
Penetrating lubricants: Primarily used for rust removal, these lubricants also benefit from the added protection of chromium coatings, especially in preventing further corrosion.
The Role of Chromium Coatings in Industrial Applications
Chromium coatings, particularly Armoloy TDC, stand out due to their unique properties. TDC, with its 98% chromium composition and cone-shaped structure, is both extremely hard and elastic. It can be applied in thin layers, enhancing the durability and efficiency of machinery without altering its structural integrity. This is evident in the case of roller bearings, where TDC coatings significantly reduce corrosion, wear and tear, and energy consumption, leading to longer service periods and more efficient material use.
Equipment owners and users observe multiple benefits from TDC, including:
- Reduced corrosion
- Reduced wear and tear on components
- Extended service periods for equipment
- Significant energy savings
- More efficient use of materials
These advantages contribute to lower operating costs, thus boosting profitability.
The coating application process temperature is below 80°C so there is no alteration to the structural or dimensional properties of the coated components.
In addition to these benefits, TDC coatings also improve the emergency run properties of bearings. In scenarios where a machine's lubrication system fails, the coated components can continue operating under a partial load for a limited period. Operators will have to shut the machine down promptly in this scenario, but an intentional shutdown versus the “seizing up” of components helps minimize or prevent costly secondary damage.
Comparative Analysis: TDC-Coated vs. Uncoated Bearings
The effectiveness of TDC coatings is markedly demonstrated in salt spray tests. Regarding corrosion reduction specifically, coating a surface with TDC protects it against water, steam, caustic solutions, and even acid to some degree. Remarkable results were noted in a salt spray test carried out according to ASTM B 117 that largely conformed to DIN 50 021.
Within just 24 hours, standard uncoated bearings showed corrosion over 95% of their surface area, while bearings made of corrosion-resistant steel displayed deterioration on 25% of their surface. In stark contrast, TDC-coated bearings showed corrosion on merely 1% of their surface area. This evidence underscores the exceptional ability of TDC coatings to protect against various corrosive agents like water, steam, caustic solutions, and to a certain extent, acid. The results clearly establish TDC coatings as a superior choice for enhancing durability and longevity in harsh industrial environments.
Benefits of Lubricants and Chromium Coatings
Regardless of whether a system or component is suited for both lubrication and chromium coatings or solely the latter, incorporating such protective coatings, like TDC, can markedly enhance their performance and durability. For those who have yet to use TDC or similar coatings, the demonstrated advantages make a compelling case for investing time to explore and possibly adopt these coatings as part of an effective protection strategy.